Tires are the only thing connecting the vehicle and the road, making them fundamental to the safety of a vehicle or aircraft. This importance is reflected in the laborious and complex nature of their production process. Ensuring production runs smoothly and safely requires robust and intelligent drive solutions. We understand how important production reliability, outstanding quality and energy-efficient drive and control technology are for tire production.
References
Protecting the environment with drive technology
Companies in the tire industry rely on an resource-friendly processes for successful and sustainable production. It goes without saying that many factors play a role in this. One of those we can influence, and which also saves you money, is the use of energy-efficient drive technology – whether in normal environmental conditions or in potentially explosive areas. In non-optimized systems, energy costs can account for up to 90% of the total life cycle costs. You can therefore use our energy-efficient drive solutions, from IE1 to IE4, to do something for the environment while also saving precious money. We can help you unlock your energy-saving potential and reduce both your energy costs and your direct and indirect CO2 emissions. Our energy-saving concept ensures a comprehensive review and consistent implementation of all the energy-saving factors that come into question. Thanks to our energy-saving tools, we can help you select and calculate energy-saving drive solutions.
Don't leave system availability to chance
Tire production is a continuous operation, and all of its processes must run smoothly and at the same high level of quality. We ensure your system can meet these stringent requirements and that it works when you need it, whether during startup, repairs, inspection, maintenance or when retrofitting the latest technologies. Leave nothing to chance – leave it to the service staff of SEW‑EURODRIVE. Your personal contact person is there for you whenever you need them. Our services are an integral part of our portfolio and are closely intermeshed with our products to ensure you can get everything you need from one place! SEW‑EURODRIVE has been synonymous with drive and automation technology expertise for more than 87 years. If you can't afford any more breakdowns, turn to the professionalism and tailored support of our services.
Find out more about Life Cycle ServicesSafety first
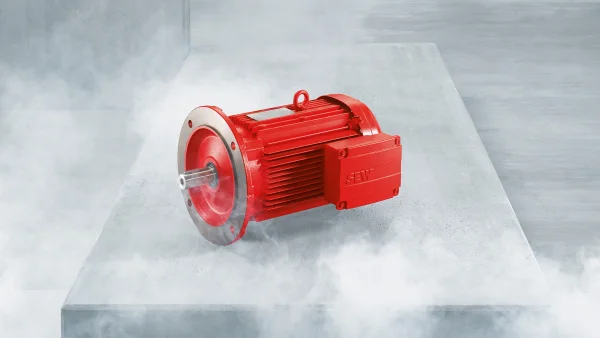
Explosive mixtures of dust and air can form when mixing rubber and manufacturing tires. Depending on the substances involved and how fine the dust is, between 60 and 2000 grams of dust per cubic meter of air can be enough to produce a dust explosion when a suitable ignition source is present. These ignition sources can also include conventional electric drive technology.
To ensure no sparks are generated that could trigger an explosion, we consistently use explosion-proof drives in systems that are operated in these high-risk conditions. Our explosion-proof gearmotors satisfy the requirements set out in EU Directive 2014/34/EU (ATEX, formerly Directive 94/9/EC). They also comply with the IEC/IECEx and HazLoc-Na® standards, which makes it easier to use our drive technology worldwide. We also offer degree of protection IP65/66, OS1 to OS4 surface protection and surface protection as an XCO® drive package.
Components and technical data
Not all tires are the same
The intended purpose is key
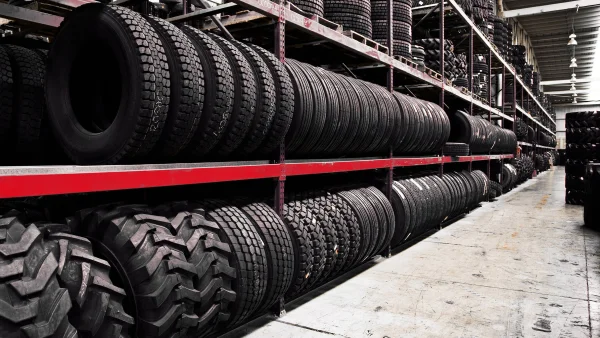
State-of-the-art tires have become an indispensable part of road travel today. Tires directly affect the fuel consumption, noise and safety of a vehicle. They maintain their traction in the winter, even at low temperatures, and displace large volumes of water in the rain so quickly that aquaplaning does not occur and we can drive safely. It is also vital to our safety that they produce the shortest possible braking distances, while, at the same time, achieving excellent mileage, even at high ambient temperatures.
In the case of motorcycle tires, traction is extremely important – particularly when turning corners. In the case of utility vehicles, tread types are an important factor, e.g. for tractors or off-road vehicles. Truck tires must be able to accommodate high loads without suffering excessive wear. Although tires used to need an inner tube to contain the air inside them, that is no longer the case – the combination of rim, tire and valve is designed in such a way that the system is self-sealing. To achieve this, the inner surface of the tire is lined with an airtight, elastic layer of rubber.
Truck tires must also meet special requirements, especially those used in the mining of base materials – in which case the tires are larger than people, weigh several hundred kilograms and can carry loads of several metric tons. As you can see, there are various types of tire for every possible application in the tire industry depending on their ultimate intended use.
Producing new tires (as opposed to retreaded tires) is a complex process for the various tire manufacturers because the end product must exhibit the characteristics outlined above, but tires are also needed in different types and sizes. The framework for a tire comprises up to 25 individual components. And because tires are sometimes used in the most adverse conditions, the production process is subject to constant quality controls.
A tire is made up of various components. We usually devote most of our attention to the rubber of the tread, but the bead, sidewall and carcass are also integral parts of a tire. Before the tread is pressed at the very end of the tire production process, the body of the tire – the carcass – must be made first. In fact, it is this stage that determines – based on how individual layers of fabric are applied – whether the tire will be radial or bias-ply. The benefits of radial tires include low rolling resistance, which reduces fuel consumption, and better directional stability during acceleration/braking. Bias-ply tires, by contrast, exhibit better driving stability and more rigid sidewalls, which are desirable characteristics in motorcycle tires, for instance.
Data and documents
You can download comprehensive documentation here.
Brochure about the tire industry (PDF, 4.4 MB)
Reference flyer – EMS for tire industry (PDF, 404 KB)
Reference flyer – Calender large gear units for tire industry (PDF, 488 KB)
More on the P‑X gear unit series
Products and solutions (PDF, 8.1 MB)