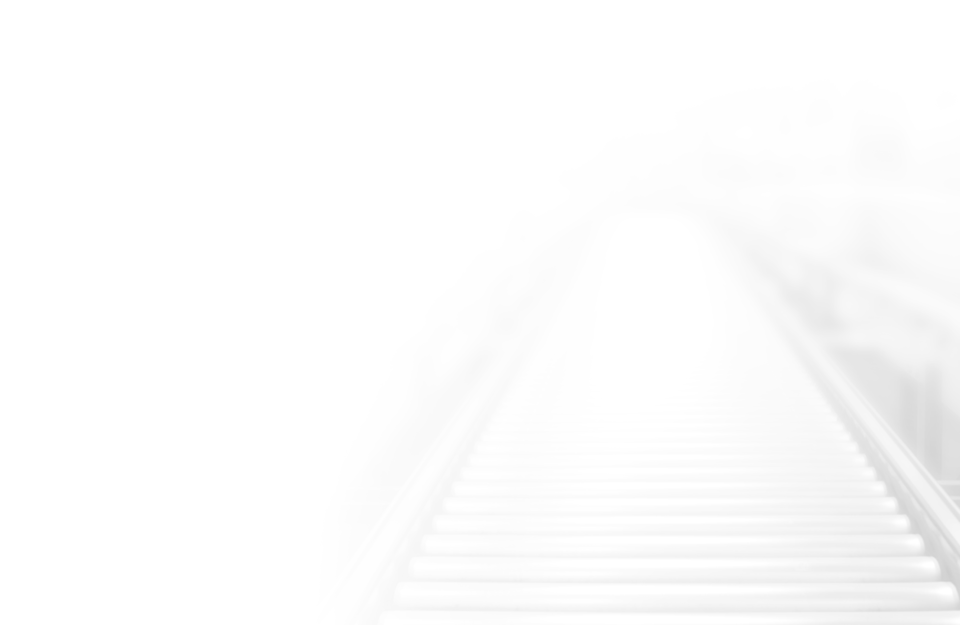
Response to line phase failure
- Menu: 4.6.9-1.1-1
- Index: 8622.4
Description
Specifies how the inverter responds to a line phase failure.
If the line input phases can be measured directly, the phase failure is monitored by direct measurement. Detecting the line phase failure takes less than 40 ms.
If the line input phases cannot be measured directly,the phase failure can only be monitored indirectly via the ripple of the DC link. If one phase fails, the ripple increases drastically. To detect the ripple, the inverter must be loaded with a base load. Detecting the line phase failure takes about 100 ms.
The following settings are possible:
Setting | Meaning |
---|---|
No response | The event is ignored. |
Warning | The inverter does not respond. The fault code is displayed via the display elements of the inverter and is output in process data. |
Application stop + output stage inhibit | The drive stops subject to speed control with the value of the Deceleration parameter (parameter group Monitoring functions > Limit values). The output stage is inhibited when motor standstill is reached. If a brake is installed, it is applied or the DynaStop® function is activated. |
Emergency stop + output stage inhibit | The drive stops subject to speed control with the value of the Emergency stop deceleration parameter (parameter group Monitoring functions > Limit values). The output stage is inhibited when motor standstill is reached. If a brake is installed, it is applied or the DynaStop® function is activated. |
Output stage inhibit | The output stage is inhibited immediately. If a brake is installed, it is applied or the DynaStop® function is activated. The drive is stopped in a non-controlled manner. |
DefaultSetting
Application stop + output stage inhibit
