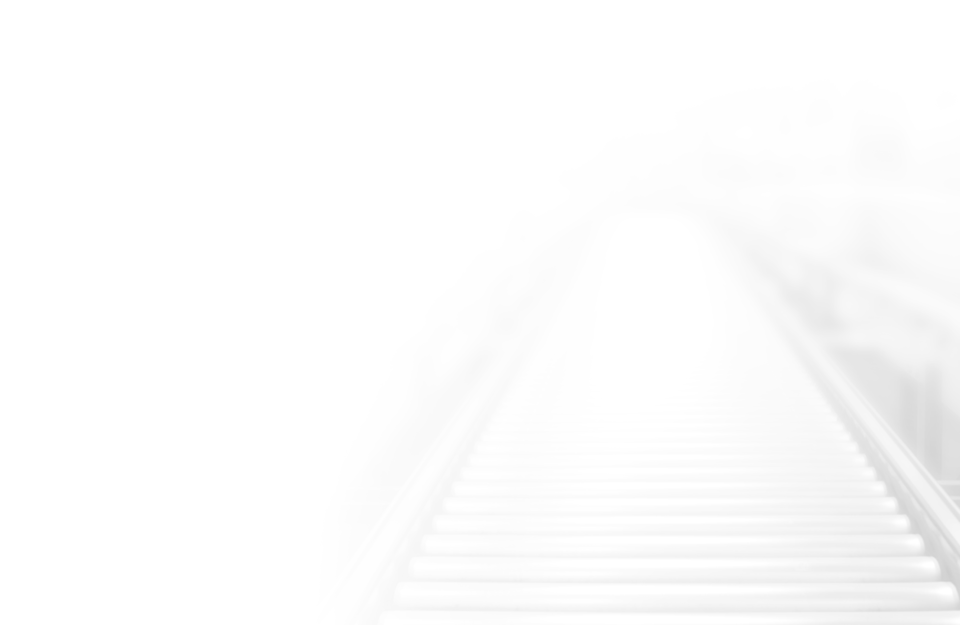
FCB 18 Rotor position identification
- Menu: 4.4.18
Description
The exact position of the rotor must be known for controlling a synchronous motor. The inverter uses the position information to generate the maximum motor torque.
FCB 18 is used for commutation detection of rotary and linear synchronous motors. Commutation can be performed with or without motor rotation. SEW‑EURODRIVE recommends to use the method with motor rotation, if possible.
For commutation, the drive must be disconnected from the load, which means also from the gear unit. If this is only possible with considerable effort or not possible at all, first perform the FCB 25 Motor parameter measurement drive function and then rotor position identification with the motor at standstill.
FCB 18 must be executed in the following cases:
- If no single-turn absolute encoder is used, each tme the inverter is switched on.
- Once, if an absolute encoder is used but the rotor position is not known. This can be the case, for example, when using a third-party motor or during startup/replacement of the encoder on a motor from SEW-EURODRIVE .
In FCB 18, hardware limit switches and software limit switches are ignored.
