Iron is the most used metal in the world. One of the most important derivatives of iron is steel. Without steel, there would be no automobiles as we know them today and no raw materials for consumer goods such as telephones, either. The most cost-effective way to manufacture steel is to produce it in an integrated steel works. Thanks to new iron and steel production methods, the prospect of manufacturing green steel is in sight.
-
Raw material handling and distribution to blast furnaces
-
Filling the steel converter
-
Handling steel scrap
-
Filling the electric arc furnace
-
Material transport using torpedo cars and slag cars.
-
Material transport using ladle cars
Raw material handling and distribution to blast furnaces
The heart of a steelworks never stops beating. Working continuously, year after year, a large blast furnace will produce over five million metric tons of raw iron yearly. To feed the furnace, huge volumes of materials need to be moved from A to B day in, day out. Lump ore, pellets, sinter, coke, and other essential raw materials are conveyed in batches to the blast furnace by a belt conveyor or an inclined elevator with winch. The supply of raw materials must not be interrupted and conveyor systems must operate perfectly. Drives from SEW-EURODRIVE run continuously at full output, and are the number one choice when system availability really matters.
Filling the steel converter
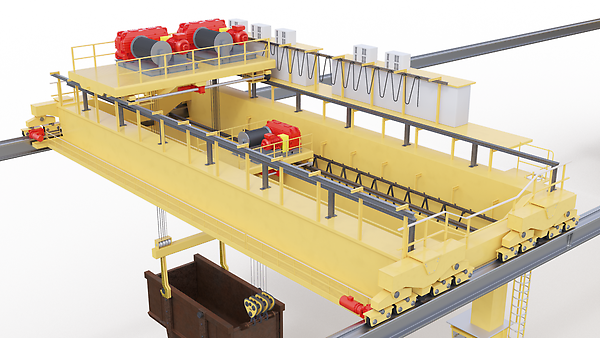
A steel converter is filled with steel scrap and molten iron from the blast furnace. Adding oxygen to this mix reduces its carbon content, ultimately turning the iron into steel. The whole process takes around half an hour. Unplanned system downtime during this crucial process step would be an absolute nightmare for any plant operator, but you can avoid that very risk by using drive technology from SEW-EURODRIVE.
Handling steel scrap
In the circular economy, steel scrap is broken down and sorted, before then being transported to steelworks by ship, train, or truck for further processing. The steel scrap is handled using huge magnets or, in the case of smaller pieces, crane grabs.
Filling the electric arc furnace
Electric arc furnaces are used in small or particularly energy-efficient, or green steelworks. They are filled with steel scrap and fitted out with electrodes. An electric current is passed through the steel scrap and melts the mass. The furnace is tilted so the molten steel can flow into a ladle car.
Material transport using torpedo cars and slag cars.
Ladle cars and torpedo cars are used to transport either molten iron or molten steel to further processing steps.
It is particularly important that the drives on these cars facilitate a reliable tilting motion when the cars are being emptied and ensure they run smoothly when operating with heavy loads.
Material transport using ladle cars
The molten steel from the converter or electric arc furnace is moved from A to B in a ladle car.
The steel will pass through several process steps in the steelworks as part of secondary and tertiary metallurgy. One well-known treatment is vacuum degassing to remove unwanted gases from the steel.
Teamwork – machine builders and SEW‑EURODRIVE
We aim to make your project successful and offer you:
- Our expertise and resources – you achieve a level of quality that sets you apart from the competition.
- High-tech solutions that minimize the particular risks in your project.
- The best delivery times on the market – we save you money and increase your flexibility.
- A comprehensive portfolio of solutions – with SEW-EURODRIVE, you will quickly find the right solution without time-consuming research or development work.
- The latest trends and innovations – ultimately, the drive solutions of tomorrow are already available today.
- Bespoke training – we prepare your employees for the most demanding projects.
- Order-relevant and user-specific documentation – benefit from the best possible conditions for a smooth startup.
- Local availability – we are always nearby thanks to our global network of plants and branches.
Products and solutions used
Further information
about drive technology in the steel industry is available here: Brochure (PDF, 43.8 MB)