Copper beech is by far the most common type of hardwood, and also the best suited for a wide range of solid wood products in Germany and Central Europe. Pollmeier Massivholz GmbH und Co. KG has therefore specialized in manufacturing timber from this type of tree.
From hydraulic to electrical drive
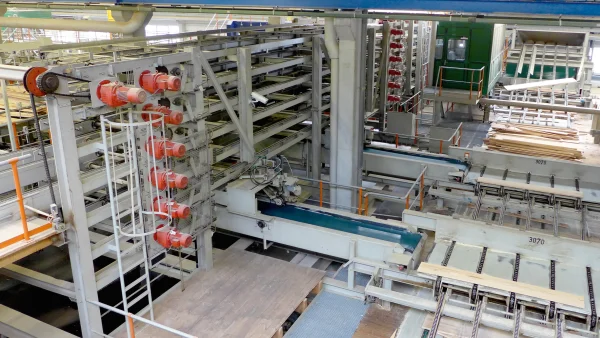
When Pollmeier’s sawmill in Malchow, in the Mecklenburg Lake District region of Germany, resumed operations in 2016 after a four-and-a-half year hiatus, the hydraulic drive of one of the two head saw s needed to be replaced. The decision was made to use an electrical drive from SEW-EURODRIVE. Company owner Ralf Pollmeier is open to this kind of change when it both leads to improved production and is ecologically sustainable. "Electrical drives are excellent for automation," explains plant engineer Winfried Riemke. "And SEW was our first choice from the start for this."
Using an electrical drive here was new territory for both us and the customer, because an electrical feed for this system had never been considered before. Pollmeier operates the largest hardwood sawmill in Europe. Roughly 80 % of the approximately 400 conveyor systems are now fitted with SEW-EURODRIVE drive technology.
"It has never let us down," explains Riemke.
"It is not just that the technology is reliable, the service is great, too. Someone with specialist expertise is on hand 24 hours a day. We are also fortunate that SEW-EURODRIVE's Güstrow Technical Office is nearby.“
From log to plank
Quality is a top priority for our customer. This begins with how the beech logs are stored when they are delivered. The lumber is then trimmed, scanned and debarked, before passing through a metal detector to prevent damage to the bandsaw blades. Only then are the logs transferred to the sawmill, where they are scanned again so as to achieve the highest possible number of planks. The head saw is the next port of call, where the logs are sawed on four sides, producing a rectangular core that can be processed into planks. The number of planks that can be obtained from a single log is determined at this semi-automatic head saw.
Electrical drive for the feed carriage
The transfer onto the feed carriage involves moving logs weighing as much as three metric tons. The operator at the controls brings the logs into the ideal position for scanning. The scanner sends the result to the controls for the transverse axes of the feed carriage. The feed carriage is driven by two ropes that are wound onto a single drum and then routed via a pulley and fed back. The rope drum sits on an axle that rests on a three-stage X3FS160 industrial helical gear units with a doubly safe design.
"Maschinenbau Malchow demanded this high level of safety in the design based on its many years of experience," says Riemke.
According to Klaus Kröner, SEW-EURODRIVE installed two DRS280S4 motors to drive the rope pulleys. These motors each have a rated power of 75 kW, and with a delta connection and operation up to 87 Hz they can achieve a shaft power of 130 kW. They generate torque ratings of up to 483 Nm and drive the rope drum via the two helical gear units.
Using braking energy constructively
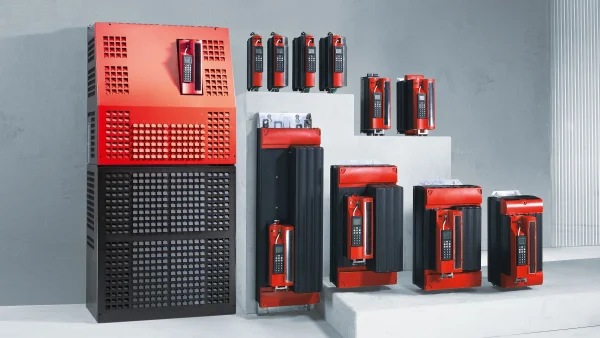
Using electric motors has resulted in considerable energy savings compared to the hydraulic solution. Braking energy is converted into electrical energy and fed back into the grid. "Current measurements put the peak motor performance at 233 kW," explains Kröner. "Peak regenerative power was 152 kW. If you go by the average drive power, which ranges between 10 and 12 kW depending on the capacity utilization of the saw, the regenerative share is as much as 40 percent."
"For practical operations, this energy recycling means that the braking process can be gentler," adds Riemke.
Components
Contact
Feel free to contact us!
Do you need advice on a specific application? Just send us a message with your questions.
Contact us now