-
By activating this video, Youtube will transfer data to the USA. More in our privacy policy.
Automation implemented efficiently
Users of state-of-the-art packaging machines need technical solutions that are both efficient and sustainable. That is why packaging machinery manufacturer HUGO BECK wanted to replace all the pneumatic systems in its "flowpack X" and "flowpack R" horizontal form, fill, and seal machine with electromechanical drive technology. Thanks to StarterSET and comprehensive extensions from SEW-EURODRIVE, it was possible to significantly reduce overall energy consumption.
The projects at a glance
Paper unwinder Paper unwinder - Packaging technology that is more sustainable
- Modular and hybrid flowpack solution that doesn't use compressed air
- Early warning for failure
- Energy management
- Packaging in paper-based materials and in air-tight film packaging
Hugo Beck Maschinenbau, plant engineering specialist for packaging technology, is constantly working to enhance its products with a view to making packaging technology more sustainable. The company therefore wanted to use SEW-EURODRIVE technology to replace the pneumatic technology previously used in its flowpack X and flowpack R horizontal form, fill and seal machines with electrical actuators. An early warning system for system failures and intelligent energy management were also to be implemented. The ultimate aim was to ensure the packaging machine could be used as a compressed-air-free, modular, and hybrid flowpack solution for both paper-based and film packaging.
Our solution in the control cabinet Our solution in the control cabinet - StarterSET 616 for HFFS including MOVIKIT® Bundle FFS
- PES intelligent energy management system
- Stepper technology including I/O System
- HMI visualization (operator panel)
- MBM model-based monitoring, parameter monitor
- Digital twin for process monitoring
- Servo technology (servomotors, servo gear units)
- Recipe management
- Integrated safety and sensor technology (STO, SLS)
- Sensor technology for print mark detection
Automation from a single source
The horizontal FFS machine, which had previously been run on compressed air, was automated using the "StarterSET 616" basic package from SEW‑EURODRIVE, along with comprehensive extensions such as Power and Energy Solutions and safety technology. As a result, it was possible to completely replace the pneumatic systems of the flowpack X with electrical actuators and extend the machine with intelligent energy management. The result is a machine with extremely low energy consumption. Perfectly coordinated software and hardware packages make the StarterSET a fully comprehensive automation solution.
Saving energy, time, and costs the smart way
Power and Energy Solutions with MOVIDRIVE® modular application inverter Power and Energy Solutions with MOVIDRIVE® modular application inverter Intelligent energy management
Combined with the MOVIKIT® software modules from SEW-EURODRIVE, the new energy storage system makes intelligent energy management possible. This makes the power supply more stable and helps bridge brief voltage dips. Peak loads are also reduced. One particular advantage is that the horizontal FFS machine is brought to a controlled stop in the case of longer power outages. As a result, the flowpack X can still be used when the local power grid is instable or even when a power outage is expected. Reducing peak loads also has another benefit, as the developers were thus able to significantly reduce the cross section of the power cable compared to the previous model. The machine's connected load and overall energy consumption have also dropped considerablyFlowpackerThe video is loading...
Energy-efficient, compact, and sustainable: this horizontal form-fill-seal machine processes up to 150 paper packages per minute—without any compressed air.
Our solution in the control cabinet - StarterSET 512 for HFFS including MOVIKIT® Bundle FFS
- MOVITRAC® advanced compact frequency inverters
- Stepper technology including I/O System
- 230 V AC single-phase current connection
- Servo technology (servomotors, servo gear units)
- Recipe management directly in the controller
- For paper packaging, up to 150 cycles per minute
- Sensor technology for print mark detection
More efficiency thanks to electrical actuators
Stepper technology (stepper motors) including I/O system instead of pneumat Stepper technology (stepper motors) including I/O system instead of pneumat Electrical actuators take the place of pneumatics
Previously, motions such as cutting and clamping in the flowpack R packaging machine were implemented conventionally, using compressed air. However, stepper motors are now used for these purposes, and are controlled with the new bus terminal from the I/O system portfolio supplied by SEW-EURODRIVE. There is therefore absolutely no need for pneumatics. Replacing the actuators that were operated by compressed air also eliminates the associated maintenance requirements. The horizontal FFS machine from Hugo Beck is now easier to integrate into the production environment and offers more flexibility in this regard, too. Furthermore, energy costs are lower with this model.
Development and startup times cut
The key to speeding up development was to use a StarterSET, which is a fully and perfectly coordinated basic package of software and hardware "made by SEW-EURODRIVE". Despite the extensive reconfigurations, the development and startup times for the packaging machine were reduced by two months, taking them down to the absolute minimum.flowpack X without pneumatics flowpack X without pneumatics - Development and startup time cut
by 2 months thanks to pre-selected basic package - Bridging of voltage dips
for up to 9.5 seconds without line voltage - Controlled cycle stop in case of power loss,
thanks to Power and Energy Solutions - Reduction in connected load
from 32 A to 16 A - Reduction in overall energy consumption
- Compressed-air-free operation
thanks to stepper technology including I/O System - Integrated temperature control
in MOVI-C® CONTROLLER UHX65
Voices from the project team
Timo Kollmann, managing director at Hugo Beck Maschinenbau
"Short distances and on-site support are clear advantages. After all, despite the considerable reconfigurations, we've been able to reduce the development times for our new and sustainable flowpack X and flowpack R packaging machine. We're already looking forward to upcoming projects with SEW‑EURODRIVE."
Jack Soreck, field sales engineer at SEW-EURODRIVE
"I'm proud we were able to both provide and utilize all the components for fully automating this sophisticated packaging machines – and all from a single source."
Our products at a glance
Close tableWe have stored a table for you here.
Good to know
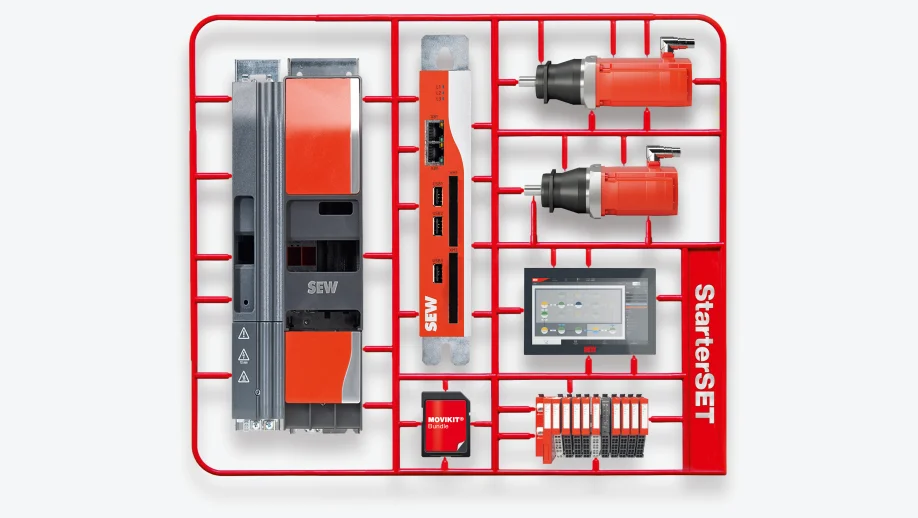
Downloads
- Brochure "StarterSET performance" (PDF, 7.5 MB)
- Brochure "StarterSET compact" (PDF, 6.7 MB)
Video and flyer
StarterSET in use
Horizontal Form Fill and Seal Machinefully automated with SEW-EURODRIVE
Downloads
- Flyer: Reference project flowpack X (PDF, 316 KB)
- Flyer: Reference project flowpack R (PDF, 2.3 MB)